Adsorber for Activated Carbon and Iron Hydroxide
DESULPHURISATION UNITS FOR BIOGAS
The removal of hydrogen sulfide (H2S) from biogas has so far received little attention. The increased requirement for environmental protection and the improvement of the reliability of the operated biogas fuels involves the removal of hydrogen sulfide from the biogas. Adsorbers with activated carbon or iron hydroxide can be the optimal solution.
THE PROCESS
For the removal of hydrogen sulfide from the biogas activated carbon and iron hydroxide are very suitable as absorbents. Both activated carbon and iron hydroxide have a high capacity for hydrogen sulfide and can guarantee a high final purity of the gas.
The adsorber is designed as a continuous system. The activated carbon is in a cylindrical container. The activated carbon pellets or pelleted iron hydroxide are flowable. The gas is introduced into the lower part of the filter and flows from the bottom upward through the cylinder. The activated carbon is fed into the cylinder from the top by a butterfly valve. An appropriate subset of activated carbon can then be easily removed on the flap at the bottom of the container. This has several advantages:
- The activated carbon inside the adsorber can be used more efficiently, i.e. the consumption of activated carbon decreases. The material flows slowly through the tank. The activated carbon (or the iron hydroxide) situated at the bottom of the cylinder is responsible for the primary purification of the gas. The carbon freshly inserted from above is responsible for the precision purification. In this way, the quality of the purification can be controlled and the carbon is steadily filled into the cylinder.
- The replacement of the carbon does not need to be affected completely. Depending on the gas quality just, a little subset is discharged and replaced by fresh activated carbon. The work expended is thus low and is not a strain.
REGENERATION AIR
By admixing a low quantity of oxygen (air) the activated carbon can be loaded much higher as the carbon is impregnated or doped with a special addition agent. The parallel processed regeneration is reached by an addition of air of approximately 1 – 3 vol. % (depending on the H2S content2S-content of the gas) to the crude gas. Elemental sulfur is developed by the reaction of hydrogen sulfide with oxygen and remains in the activated carbon.
While the binding of the hydrogen sulfide is carried out by adsorption in the activated carbon and regeneration directly according to the equation
H2S + ½ O2 → S + H2O
occurs, run the cleaning step and the regeneration of the iron hydroxide by the following chemical reactions:
Cleaning
2 Fe(OH)3 + 3 H2S → Fe2S3 + 6 H2O ∆ HR = – 63 kJ (1)
Regeneration
Fe2S3 + 1,5 O2 + 3 H2O → 2 Fe(OH)3 + 3 S ∆ HR = ‑ 603 kJ (2)
In practice, however, no difference in the operation is found.
The parallel proceeded regeneration is obtained by the addition of approximately 1 –3 % by volume air (depending on the H2S content of the gas) to the raw gas. A signal is taken from the gas volume-measuring device to adjust the admixture quantity. A dosing unit adds the regeneration air according to the actual flowing gas quantity.
The dosing installation for regeneration air includes:
- Control unit for the air admixture with non-return valve and magnetic valve
- Temperature monitoring of the pure gas
- Measuring the charged air quantity inflow
- Display for volume flow, analogue
- Potential-free output for notice of the malfunction
FUNCTION OF THE AIR ADMIXTURE DEVICE
The gas quantity flowing through the desulphurisation unit is measured by the gas quantity measuring device. In a proportional way, a certain air quality of approximately 1 – 3 vol. % is admixed via a speed-controlled side channel blower. This air quantity is measured as well. The signal as well as the gas quantity is sent to the control device. This control device compares the gas quantity and the air quantity and keeps a constant gas/ air quantity ratio. The air admixture process is stopped as soon as an exceedance of a predetermined limit value occurs.
A shutdown of the air admixture process is also affected if the gas temperature at the outlet of the desulphurisation unit is higher than 60 °C.
DESULPHURISATION UNITS FOR BIOGAS
Example Unit
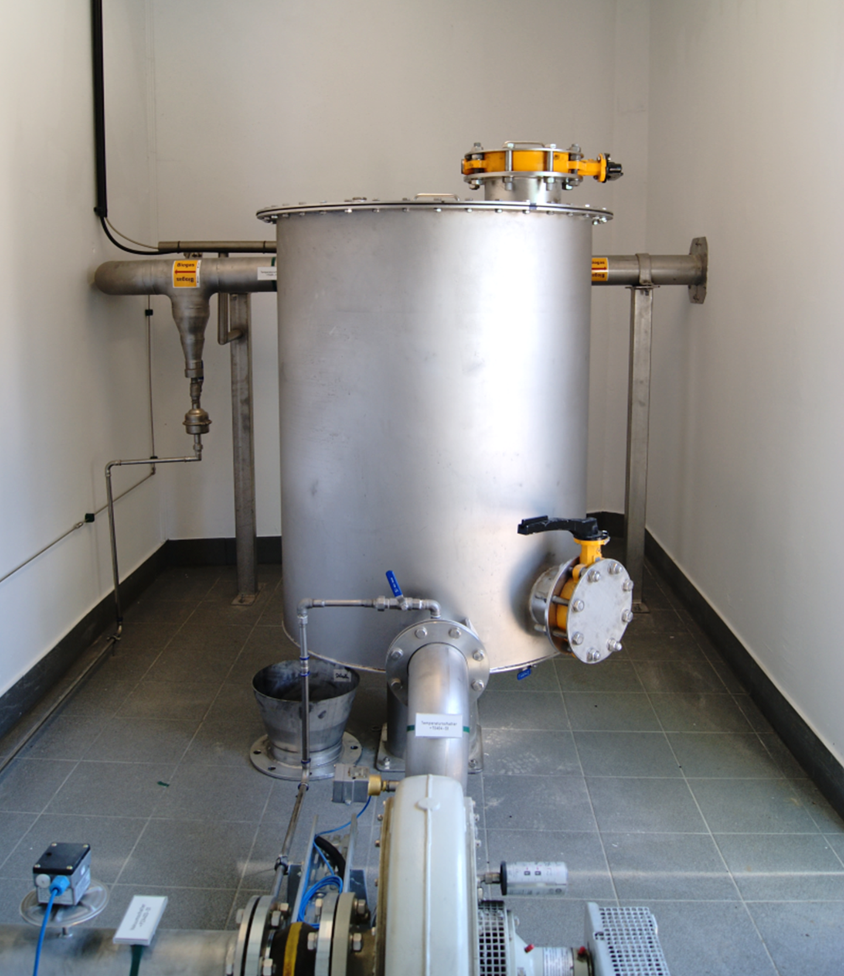
Activated Carbon Adsorber For Biogas Plant
General Information
Hydrogen sulphide content
Crude gas, max. | : | 1000 ppm |
Cleaned gas | : | < 10 ppm |
Maximum allowable operating pressure | : | 100 mbar |
Permissible temperature range | : | 5 – 35 oC |
Permissible relative gas humidity | : | < 70 % |
Pressure loss | : | app. 10 mbar |
Adsorption tank
Material | : | 1.4571 |
Feed hopper for activated carbon | : | DN 200 |
Butterfly Valve | : | DN 200 |
Butterfly valve for removal | : | DN 150 |
Option | ||
Heat insulation | : | 100 mm mineral wool |
Panelling | : | Aluminium sheet |
Regeneration air admixture
Purpose | : | provision of regeneration air for optimal utilisation of the activated charcoal |
Air Compressor | ||
– Design type | : | side channel blower |
– Volume flow air | : | max. 10 m³/h |
– Pressure | : | max. 120 mbar |
Air Flow Meter | : | variable area flow meter |
– Measuring range | : | 0.9 – 9m³/h |
Flow and temperature monitors | : | 1 |
Mechanical non return valve | : | ½” |
Solenoid valve | : | ½” |
Ball valve | : | ½” |
Control unit | : | 400 x 400 x 210 mm |
Size Chart
ADSORBER FOR ACTIVATED CHARCOAL AND IRON HYDROXIDE
Size | m³/h | 120 | 200 | 280 | 420 | 500 | |
Height unit | Hges | mm | 1.820 | 1.870 | 1.920 | 1.970 | 1.990 |
Diameter unit | ØZyl | mm | 960 | 1.200 | 1.500 | 1.750 | 1.900 |
Weight unit – empty | mL | kg | 350 | 460 | 570 | 690 | 770 |
Gas nozzle inlet | DN | DN | 80 | 100 | 125 | 150 | 150 |
Gas nozzle outlet | DN | DN | 80 | 100 | 125 | 150 | 150 |
Feeding nozzle for pellets | DN | DN | 150 | 150 | 150 | 150 | 150 |
Removal nozzle for pellets | DN | DN | 150 | 150 | 150 | 150 | 150 |
ADSORPTION AGENTS FOR ADSORBER
Activated carbon – doped
Raw material base | : | Charcoal |
Properties | Doped activated carbon with alkali and alkaline earth Fully open pore system | |
Spent activated carbon | : | Use as a fertilizer additive possible |
Diameter pellets | : | 4 mm |
Water content | : | < 10 % |
Bulk density | : | 455 ± 20 kg/m³ |
BET surface | : | > 850 m²/g |
Micropore volume | : | > 0.35 ml/g |
ALTERNATIVE
Raw material base | : | Iron hydroxide |
Properties | Pellets | |
Diameter pellets | : | 2 – 8 mm |
Length | : | 2 – max. 20 mm |
Active substance | : | Iron(III)-oxidhydrate |
Iron content (Fe3+) | : | ca. 20 % based on the dry matter |
Dry matter content | : | min. 80 % |
Bulk density | : | 570 ± 80 kg/m³ (loose bed), app. 85 % TS 610 ± 100 kg/m³ (compacted bed), app. 85 % TS |
Initial Filling Chart for Celsigas Adsorber
REQUIRED INITIAL FILLING
SIZE | m³/h | 120 | 200 | 280 | 420 | 500 |
Activated charcoal | kg | 340 | 530 | 820 | 1,110 | 1,310 |
Iron hydroxide | kg | 420 | 650 | 1,000 | 1,380 | 1,620 |
0 Comments